About Us
In 1997, a team of experienced professionals from the chemical industry founded Cymer, which is now a privately owned company. The following year, they built a plant in Decatur, TN, and began operating primarily as a contract manufacturer. Over time, Cymer grew its operations and gained a reputation as a leading manufacturer of specialized chemicals.
In 2017, the company made strategic acquisitions by acquiring GP Chemicals Inc. in New Jersey, the specialty chemical plant of Fujifilm Hunt Chemicals, U.S.A. in Dayton, Tennessee, and several polymer technologies.
Today, we are committed to ensuring diversity in chemical suppliers and supporting industry advances in chemistry worldwide.

150+
Chemicals
36+
Partner Countries
342
Years of Chemistry
Partner with Cymer Chemicals
Key Milestones & Dates
- 1997 - Cymer, LLC was formed
- 2002 - Added additional reactors and overhead systems
- 2007 - added a 10,000 square foot warehouse
- 2008 - major equipment and infrastructure upgrades
- 2014 - added a 2,000 sq/ft lab, another 10,000 sq/ft Warehouse and a DMA bulk storage and transfer facility
- 2017 - Purchased the FUJIFILM Hunt Chemicals U.S.A. facility in Dayton, TN
- ISO 9001:2015 certified through DQS; BR#: 10016110 QM15
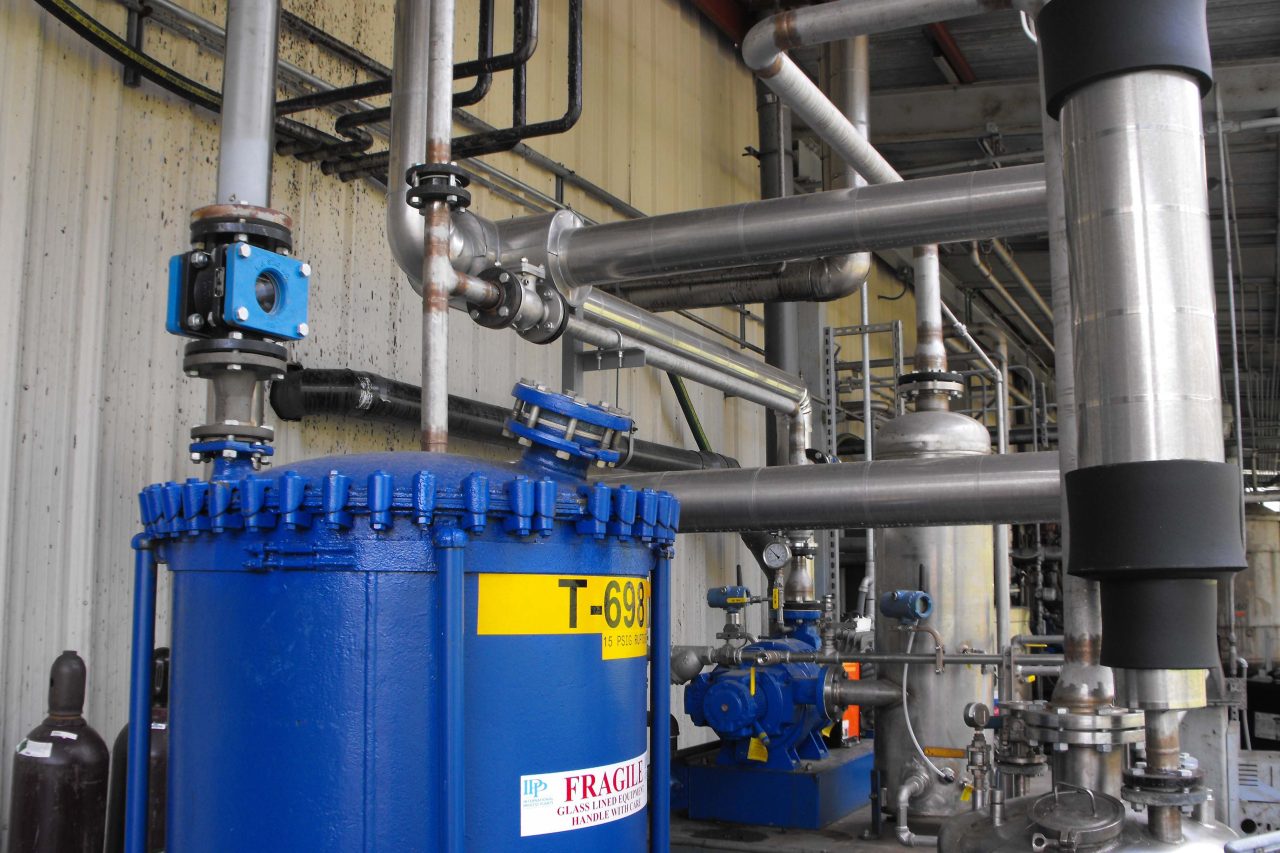
Partnerships and Communication
We Are Customer Focused
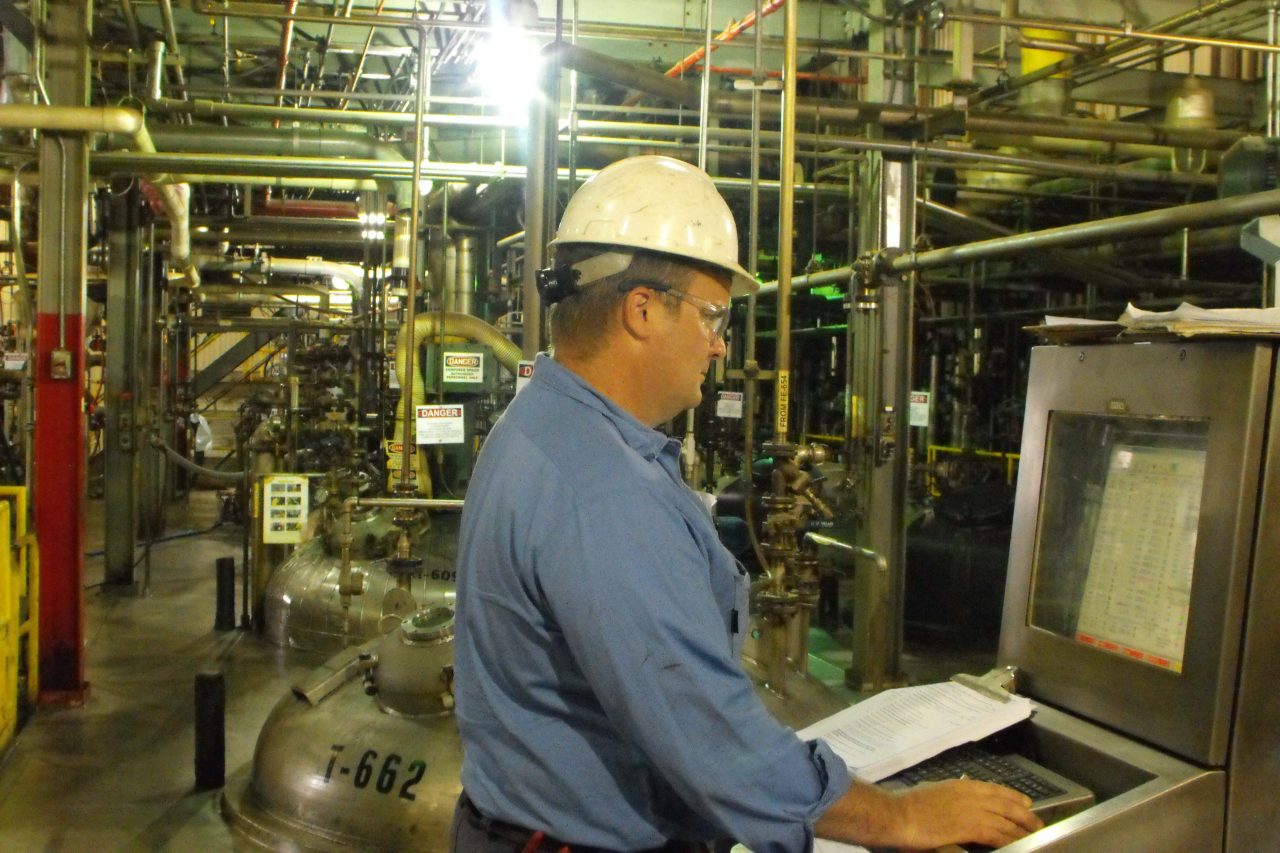
Through our years of supporting clients in custom chemical manufacturing, we have established strong partnerships within the industry.
As part of our Customer Policy, we maintain a collaborative liaison with our customers, from the conception of the production process to the delivery of the final products. Our operational proficiency has earned us a highly sought-after position as a partner in custom-made chemical manufacturing.
With expertise in both existing chemical processes and developmental projects, we can collaborate with multiple individuals, agencies, and companies to seamlessly integrate chemical design, assembly, testing, and production. We have earned a reputation as a reliable, effective, and efficient chemical manufacturer.
At Cymer, we believe in providing top-notch customer support right from the beginning of the product planning stage. Advance Product Quality Planning (APQP) is a structured method where we define and establish the necessary steps to ensure that the final product meets the customer’s goals, requirements, and expectations.
APQP involves 75% upfront planning and 25% implementation through production, which helps us determine customer satisfaction and continuous improvement over time.
APQP facilitates communication between our team and the customer to clarify requirements, translating into more detailed specifications. By doing so, we can ensure that we deliver products that meet and exceed our customer’s expectations.
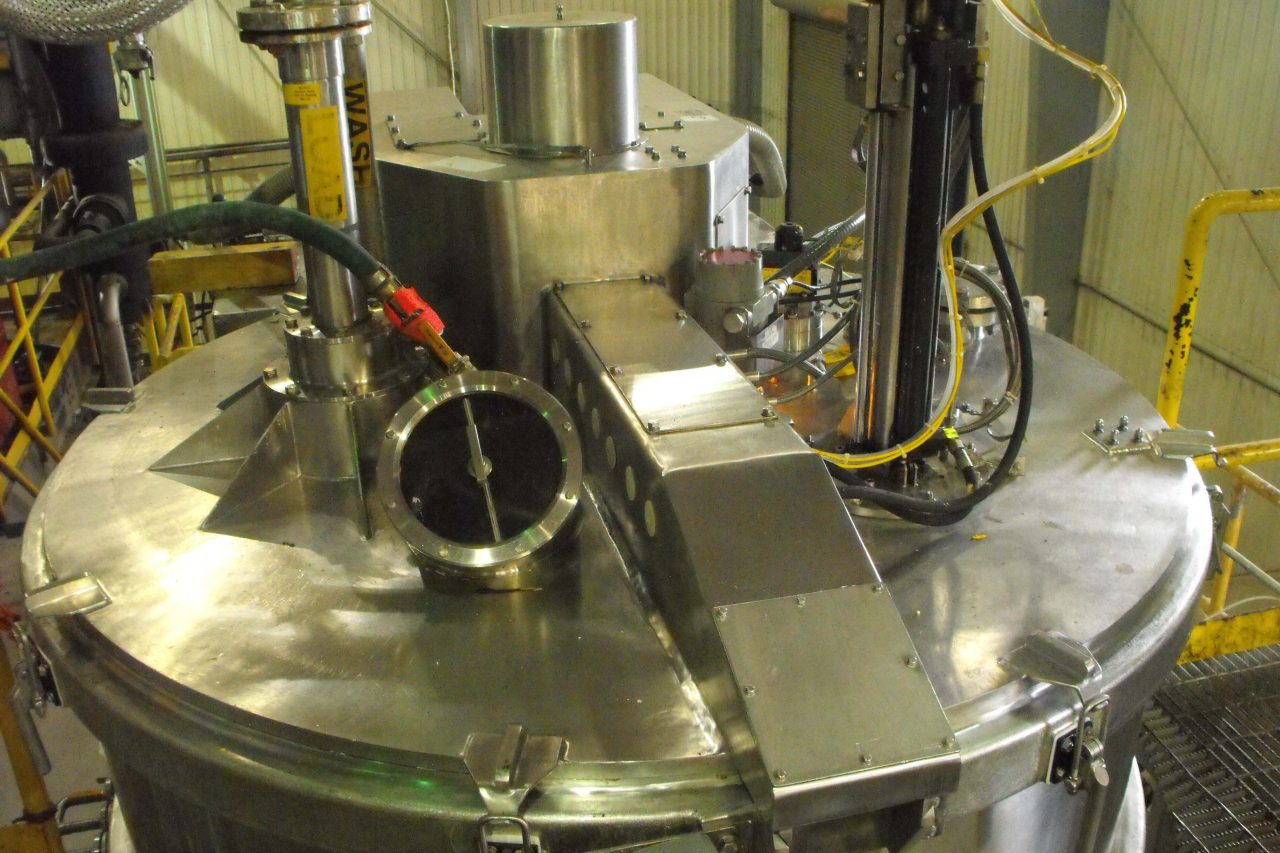